In today's competitive market, sourcing aluminium effectively is crucial for the success of any business involved in manufacturing, construction, or product development. Aluminium's versatile properties make it a material of choice for countless applications, from lightweight components in the aerospace industry to robust structures in construction. However, the process of procuring aluminium is fraught with potential pitfalls that can lead to costly mistakes if not navigated carefully. Understanding these common missteps can be the key to ensuring both the quality and cost-effectiveness of your projects.
This article aims to shed light on the most prevalent mistakes businesses make when sourcing aluminium, with a focus on three critical areas: supplier credentials and certifications, selecting the appropriate aluminium grade, and managing delivery and logistics considerations. Many businesses overlook the importance of verifying supplier credentials, which can lead to compliance issues and quality concerns down the line. Additionally, choosing the right aluminium grade for specific applications is essential, as the wrong choice can compromise the integrity and performance of the final product. Lastly, ignoring the logistics of delivery can result in delays and increased costs, impacting project timelines and budgets. By addressing these areas, this article will provide valuable insights to help businesses make informed decisions, thereby optimising their aluminium sourcing strategies. Whether you're working with local vendors or larger aluminium suppliers in Sydney, understanding these key considerations is essential for achieving success.
Overlooking Supplier Credentials and Certifications
In the ever-evolving landscape of global commerce, the importance of scrutinising supplier credentials and certifications cannot be overstated. Ensuring that your suppliers meet the highest standards is a matter of compliance and a strategic decision that can significantly impact the success and reputation of your business. Below, we delve into why overlooking these critical aspects can be detrimental and how they form the foundation of a robust supply chain.
Understanding Supplier Credentials
Supplier credentials encompass a wide array of information that verifies a supplier's ability to deliver products or services that meet your business's needs. These credentials can include business licenses, financial records, track records of previous contracts, and other forms of professional accreditation. Failing to thoroughly vet these credentials can expose your business to numerous risks, including financial instability of the supplier, poor product quality, and unreliable delivery schedules.
- Business Licences and Registrations: Ensuring that your supplier holds the necessary business licences and registrations is fundamental. These documents are a testament to the supplier's legitimacy and compliance with local and international trade laws. Overlooking these can lead to partnerships with fraudulent or non-compliant entities, resulting in legal complications.
- Financial Stability Assessments: A supplier's financial health is a crucial indicator of their ability to fulfill long-term contracts. Requesting financial statements and credit reports can provide insights into their stability and reliability. Neglecting this step may lead to unexpected disruptions in your supply chain if the supplier faces insolvency.
The Role of Certifications in Supplier Evaluation
Certifications serve as a quality assurance mechanism, indicating that a supplier adheres to industry standards and best practices. They are often awarded by recognised authorities and can cover areas such as quality management, environmental compliance, and occupational health and safety.
- Quality Management Certifications (e.g., ISO 9001): These certifications demonstrate that a supplier has implemented robust quality management systems. Partnering with a certified supplier reduces the risk of receiving subpar products and enhances your own business's credibility.
- Environmental and Social Responsibility Certifications: With increasing emphasis on sustainable and ethical business practices, certifications like ISO 14001 for environmental management or Fair Trade certifications are becoming vital. Overlooking these can harm your business's reputation, especially in industries where consumers are environmentally and socially conscious.
- Industry-Specific Certifications: Depending on your industry, there may be additional certifications that are critical. For instance, in the food industry, HACCP (Hazard Analysis and Critical Control Points) certification is essential to ensure food safety. Ignoring such certifications can lead to severe consequences, including product recalls and damage to brand reputation.
Risks of Ignoring Supplier Credentials and Certifications
The repercussions of neglecting to verify supplier credentials and certifications are manifold. Beyond the immediate risks of non-compliance and financial instability, there are broader implications for your business's operational efficiency, customer satisfaction, and brand image.
- Operational Disruptions: Unverified suppliers may fail to deliver consistently, leading to production delays and potential financial losses. Ensuring that suppliers have the necessary credentials reduces the likelihood of such disruptions.
- Legal and Regulatory Consequences: Partnering with non-compliant suppliers can result in legal penalties and damage to your business’s standing with regulatory bodies. Maintaining a thorough verification process helps safeguard against these risks.
- Diminished Customer Trust: Customers expect businesses to uphold high standards. If a supplier’s lack of credentials leads to product failures or ethical breaches, your customers may lose trust in your brand, leading to decreased sales and customer loyalty.
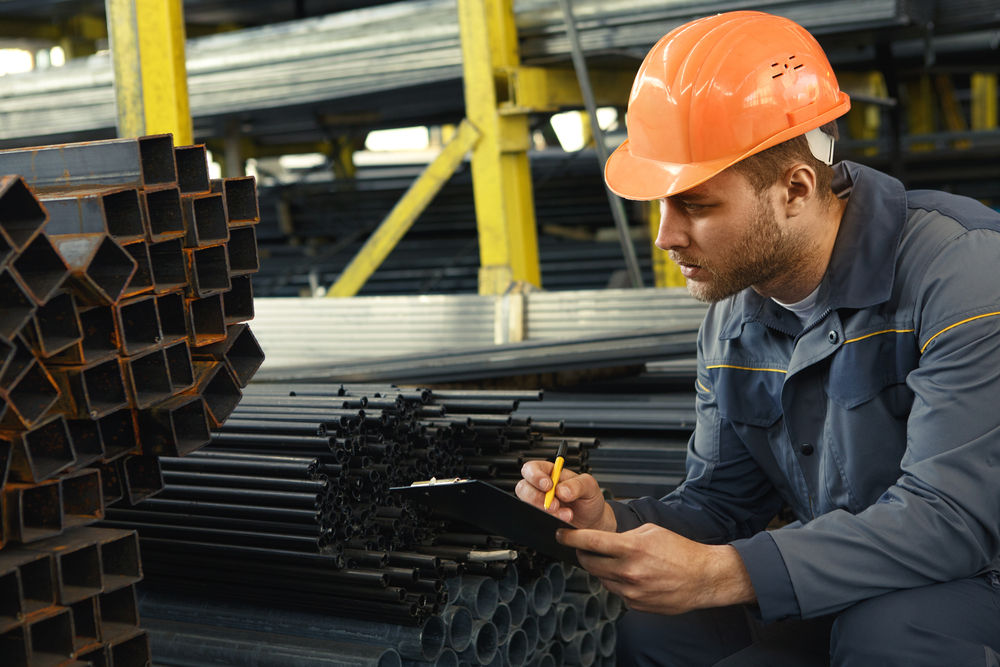
Failing to Choose the Right Aluminium Grade for Your Needs
When sourcing aluminium for your business, selecting the appropriate grade is crucial to ensure the success of your project. Aluminium is a versatile metal that comes in various grades, each with unique properties suited for specific applications. Choosing the wrong grade can lead to increased costs, compromised structural integrity, and product failures. Below, we delve into common pitfalls associated with selecting the wrong aluminium grade and provide guidance on making informed decisions.
Understanding Aluminium Grades
Aluminium is classified into different grades based on its alloy composition and temper. The grade determines the metal’s strength, corrosion resistance, workability, and other characteristics. Some of the most commonly used aluminium grades include:
- 1000 Series: Known for its high corrosion resistance and excellent workability, this series is composed of 99% or higher aluminium content. It is ideal for applications where corrosion resistance is more critical than strength, such as chemical equipment and food processing.
- 2000 Series: Often used in aerospace applications, this series is alloyed with copper. It offers high strength but lower corrosion resistance compared to other grades, making it suitable for high-stress environments where durability is paramount.
- 3000 Series: Manganese is the principal alloying element in this series. It is commonly used in beverage cans and roofing sheets.
- 5000 Series: This series is alloyed with magnesium, offering good corrosion resistance in marine environments and high strength. It is suitable for applications like shipbuilding and automotive manufacturing.
- 6000 Series: Featuring silicon and magnesium, this versatile series exhibits good corrosion resistance and moderate strength. It is commonly used for structural applications and in the construction industry.
- 7000 Series: Known for its high strength due to the presence of zinc, this series is widely used in aerospace and sporting equipment.
Common Mistakes in Grade Selection
- Overlooking Corrosion Resistance Needs
- One of the frequent errors is underestimating the importance of corrosion resistance for the intended application. For instance, using a 2000 series alloy in a marine environment can lead to rapid deterioration. Always consider the environmental exposure your product will face and choose a grade that offers adequate corrosion resistance.
- Misjudging Strength Requirements
- Selecting a grade that does not meet the strength requirements of your project can lead to structural failures. For heavy-duty applications, such as aircraft components or high-load-bearing structures, opting for a high-strength grade like the 7000 series is essential. Conversely, using such a high-strength grade for applications that do not require it can unnecessarily increase costs.
- Ignoring Workability and Formability
- Different aluminium grades offer varying levels of workability and formability. For projects requiring intricate shapes or extensive machining, such as automotive parts, choosing a grade with high formability, like the 3000 series, is crucial. Selecting a grade with poor workability can lead to increased manufacturing costs and production delays.
- Not Considering Weldability
- If welding is part of your manufacturing process, selecting a grade with poor weldability can compromise joint integrity. The 6000 series, for example, is known for its good weldability, making it a preferred choice in construction and architectural applications.
How to Choose the Right Grade
- Assess Your Application Needs: Start by evaluating the specific requirements of your project, including strength, corrosion resistance, formability, and weldability.
- Consult with Experts: Engaging with metallurgists or materials engineers can provide insights into the most suitable aluminium grade for your application, especially for complex projects.
- Consider Long-term Performance: While initial costs are a consideration, focusing on the long-term performance and durability of the aluminium can prevent costly repairs and replacements down the line.
- Sample Testing: Where possible, conduct sample testing on various grades to determine their suitability under simulated operational conditions.
Ignoring Delivery and Logistics Considerations
When sourcing aluminium, particularly in a competitive market, overlooking delivery and logistics can lead to significant challenges and inefficiencies for your business. Understanding and planning for these considerations is essential to ensure smooth operations and cost-effectiveness. Below are key aspects to keep in mind to avoid common pitfalls in delivery and logistics.
Choosing the Right Supplier Location
Proximity to Your Business
Selecting a supplier close to your operation can greatly reduce transportation costs and delivery times. While it might be tempting to go for the cheapest supplier, if they are located far from Sydney, the additional freight costs and potential delays could outweigh the initial savings.
Local Versus International Suppliers
Local suppliers can often offer more reliable delivery schedules and easier communication. International suppliers, although sometimes cheaper, might introduce complexities such as customs clearance, variable shipping times, and higher risks of damage during transit.
Evaluating Transportation Options
Mode of Transport
Consider the mode of transport that best suits your needs. For large, bulk orders, sea freight might be more economical, though slower. For faster delivery, road or air freight is preferable but can be more costly. Understanding the trade-offs between cost and speed is crucial for aligning with your production schedules.
Transportation Insurance
Ensure that your aluminium shipments are insured during transit. Damage or loss of goods can be a significant setback, affecting timelines and budgets. Confirm whether the supplier provides insurance or if you need to arrange it independently.
Scheduling and Lead Times
Accurate Forecasting
Develop a clear understanding of your demand patterns to provide accurate forecasts to your suppliers. This ensures they can meet your needs promptly and reduces the risk of delays.
Buffer Time
Always factor in buffer time beyond the estimated delivery dates. Unforeseen circumstances such as natural disasters, geopolitical events, or supplier issues can lead to delays. Having a buffer allows you to maintain operations without disruptions.
Handling and Storage Needs
Receiving and Inspection Procedures
Establish a robust process for receiving and inspecting deliveries. Check the aluminium for any damage or discrepancies in the order quantity immediately upon receipt.
Storage Requirements
Plan for appropriate storage facilities for your aluminium supplies. Aluminium must be stored in a dry, temperature-controlled environment to prevent corrosion or degradation. Adequate storage ensures the material remains in optimal condition for use.
Supplier Communication and Relationship Management
Regular Communication
Maintain open lines of communication with your suppliers. Regular updates on order status, potential delays, or changes in delivery plans can help you adjust your logistics plans proactively.
Building Strong Relationships
Develop strong relationships with your suppliers. A reliable partnership can lead to more flexible terms, priority treatment, and better problem resolution, ensuring that logistics run smoothly even when challenges arise.
In conclusion, sourcing aluminium for the extal requires a strategic approach to avoid common pitfalls that can impact the success of your business operations. Overlooking supplier credentials and certifications can lead to quality issues and compliance risks, underscoring the importance of conducting thorough due diligence. Ensuring suppliers are reputable and certified guarantees that your aluminium meets industry standards and is reliable for production. Additionally, selecting the right aluminium grade tailored to your specific needs is crucial; a misstep here can result in material inefficiencies and compromised product quality. Each aluminium grade has distinct properties that suit different applications, and aligning these with your project requirements can optimise performance and cost-effectiveness. Lastly, ignoring delivery and logistics considerations can disrupt your supply chain, causing delays and escalating costs. Collaborating with suppliers who offer reliable and efficient delivery services can safeguard against these disruptions and support your operational timelines.