In the ever-evolving world of manufacturing and construction, aluminium stands out as a versatile and essential material, known for its strength, lightweight nature, and resistance to corrosion. As a business owner operating in Sydney and sourcing materials from across Australia, partnering with aluminium suppliers in Sydney ensures access to high-quality materials for your projects. Understanding the different grades of aluminium available is vital for ensuring the highest quality in your applications.
This article delves into the diverse range of aluminium grades accessible in the Australian market, providing you with the insights needed to make informed decisions for your specific applications. From aerospace to construction, automotive to consumer electronics, aluminium finds its place in a myriad of industries. Each application demands a unique set of properties, and selecting the right grade of aluminium can significantly impact the performance, durability, and cost-effectiveness of your finished product. We will explore the most commonly used aluminium grades in Australia, including their specific characteristics, applications, and advantages. Additionally, we will discuss the importance of selecting the appropriate grade to meet regulatory standards and enhance sustainability. Whether you are looking to optimise the structural integrity of a high-rise building or seeking the perfect alloy for a lightweight vehicle component, this comprehensive guide will equip you with the knowledge to navigate the complex world of aluminium grades effectively.
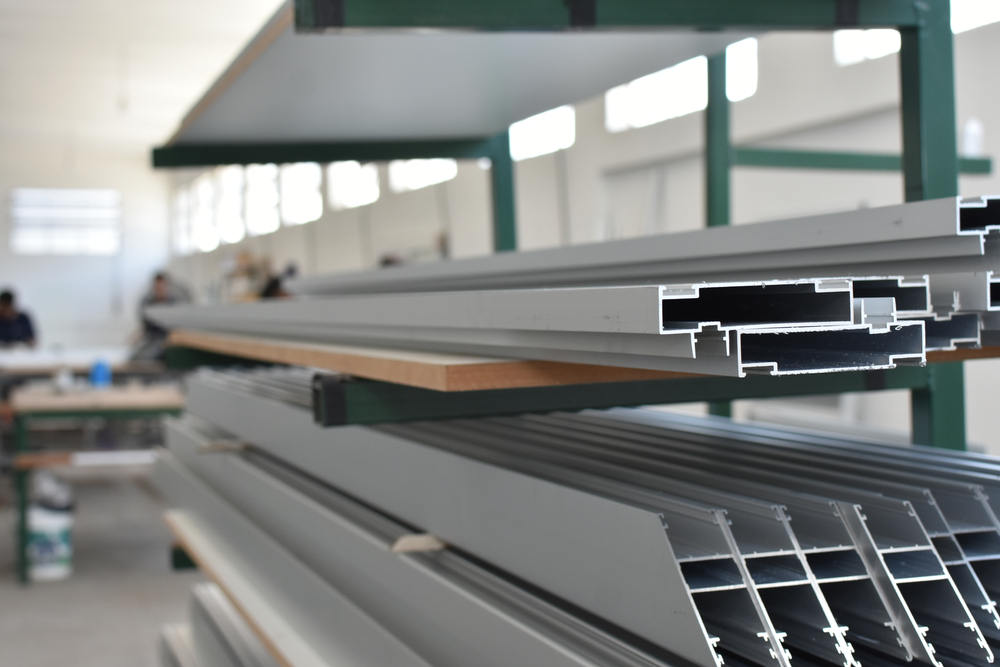
An Overview of Aluminium Grades: What’s Available in Australia
Aside from being a versatile and widely used metal, aluminium is known for its lightweight, corrosion resistance, and excellent conductivity. In Australia, various grades of aluminium are available to cater to different industrial, commercial, and residential applications. This section provides a comprehensive overview of the aluminium grades accessible in the Australian market, highlighting their properties, uses, and availability.
Understanding Aluminium Alloys
Aluminium is rarely used in its pure form; instead, it is often combined with other elements to form alloys, enhancing its mechanical properties. Aluminium alloys are classified using the Aluminium Association (AA) designation system, which categorises them into series based on the main alloying elements.
1. Series 1000: Pure Aluminium
Characteristics:
- Composed of 99% or higher aluminium content.
- Excellent corrosion resistance.
- High thermal and electrical conductivity.
- Soft and ductile.
Applications:
Used primarily in electrical and chemical applications due to its conductivity and resistance to corrosion. Common products include electrical conductors and chemical processing equipment.
2. Series 2000: Aluminium-Copper Alloys
Characteristics:
- High strength.
- Good machinability.
- Lower corrosion resistance.
Applications:
Often used in aerospace and automotive industries where strength is critical. Typical applications include aircraft structures and truck components.
3. Series 3000: Aluminium-Manganese Alloys
Characteristics:
- Good corrosion resistance.
- Moderate strength.
- Excellent workability.
Applications:
Ideal for applications where a combination of strength and corrosion resistance is required, such as in beverage cans, roofing sheets, and cooking utensils.
4. Series 4000: Aluminium-Silicon Alloys
Characteristics:
- High wear resistance.
- Lowered thermal expansion.
- Good weldability.
Applications:
Commonly used in automotive parts, architectural structures, and welding wire. The low thermal expansion makes them suitable for use in engine components.
5. Series 5000: Aluminium-Magnesium Alloys
Characteristics:
- Excellent corrosion resistance.
- High strength.
- Good weldability.
Applications:
Widely used in marine environments and for structural applications. Common products include shipbuilding materials, pressure vessels, and bridges.
6. Series 6000: Aluminium-Magnesium-Silicon Alloys
Characteristics:
- Good mechanical properties.
- Excellent corrosion resistance.
- Ease of extruding.
Applications:
Commonly found in construction and structural applications, such as in window frames, automotive parts, and railings. This series is known for its versatility and is one of the most widely used in Australia.
7. Series 7000: Aluminium-Zinc Alloys
Characteristics:
- Very high strength.
- Good fatigue resistance.
- Lower corrosion resistance without additional treatment.
Applications:
Primarily used in high-performance applications such as aircraft, aerospace structures, and sporting equipment. Their high strength-to-weight ratio makes them ideal for these demanding environments.
8. Series 8000: Other Alloying Elements
Characteristics:
- Composed of other elements such as iron and lithium.
- Specialised properties tailored for specific applications.
Applications:
Used in niche markets where specific properties are required, such as in electrical cables and lithium battery foils.
Availability and Sourcing in Australia
The availability of these aluminium grades in Australia is supported by a robust network of local manufacturers and suppliers, including prominent companies that specialise in producing and distributing aluminium products. Businesses can source aluminium in various forms, such as sheets, plates, extrusions, and bars, tailored to meet the requirements of diverse industries.
Aluminium grades are available from major suppliers across Australia, including locations in Sydney, Melbourne, Brisbane, and Perth. These suppliers ensure that businesses have access to a wide range of products, catering to both standard and custom specifications.
Key Properties and Uses of Popular Aluminium Grades
Aluminium is a versatile and widely used material across various industries in Australia, known for its remarkable properties such as lightweight, corrosion resistance, and excellent thermal and electrical conductivity. In this section, we explore the key properties and uses of the most popular aluminium grades available in the Australian market, providing insights into their unique characteristics and typical applications.
1. Aluminium 1100
Properties:
Aluminium 1100 is one of the purest aluminium grades, with a minimum of 99% aluminium content. It boasts excellent corrosion resistance, formability, and thermal and electrical conductivity. This grade is highly workable and can be easily welded, making it ideal for applications requiring intricate forming and bending.
Uses:
Aluminium 1100 is commonly used in chemical and food processing industries because of its high ductility and excellent resistance to corrosion. Its primary applications include kitchen utensils, heat exchangers, and decorative trim. Additionally, it is utilised in the production of sheet metal for architectural purposes, such as roofing and cladding.
2. Aluminium 2024
Properties:
Aluminium 2024 is known for its high strength-to-weight ratio, making it one of the strongest aluminium alloys available. It contains copper as its primary alloying element, which enhances its strength and fatigue resistance. However, this grade is less corrosion-resistant compared to other aluminium alloys and requires protective coatings when used in harsh environments.
Uses:
The aerospace industry heavily relies on Aluminium 2024 for structural applications, including aircraft fuselage and wing components, due to its excellent strength and fatigue resistance. It is also used in military vehicles and equipment, as well as in the manufacturing of high-performance sports equipment where strength and durability are essential.
3. Aluminium 3003
Properties:
As an alloy primarily containing manganese, Aluminium 3003 offers a good balance of strength and workability. It demonstrates excellent corrosion resistance and moderate strength, making it more durable than pure aluminium grades. Additionally, it is easily formable and weldable.
Uses:
Aluminium 3003 is widely used in the manufacturing of cooking utensils, chemical equipment, and storage tanks due to its resistance to corrosion, especially in humid environments. It is also popular in the HVAC industry for heat exchangers and air conditioning components, as well as in the automotive industry for fuel tanks and other vehicle parts.
4. Aluminium 5052
Properties:
Aluminium 5052 is an alloy containing magnesium and chromium, providing it with exceptional corrosion resistance, particularly in marine environments. It offers good weldability and moderate to high strength compared to other non-heat-treatable alloys. Additionally, it maintains excellent formability, making it suitable for complex shapes and designs.
Uses:
Due to its superior corrosion resistance in saltwater, Aluminium 5052 is extensively used in marine applications, including boat hulls and decks. It is also employed in the construction industry for roofing and siding, as well as in the manufacture of pressure vessels, tanks, and other containers that require high corrosion resistance.
5. Aluminium 6061
Properties:
Aluminium 6061 is a heat-treatable alloy known for its excellent mechanical properties and versatility. It contains magnesium and silicon as its major alloying elements, which enhance its strength, corrosion resistance, and machinability. It can also be easily welded and anodised for additional protection.
Uses:
This grade is a favorite in the construction and structural industries, where it is used for building frames, bridges, and scaffolding due to its high strength and durability. It is also popular in the automotive and aerospace sectors for manufacturing vehicle frames and aircraft components. Additionally, Aluminium 6061 is used in the production of consumer goods such as bicycles and recreational equipment.
6. Aluminium 7075
Properties:
Aluminium 7075 is one of the highest strength aluminium alloys available, primarily containing zinc as its alloying element. It offers exceptional strength and toughness, rivaling some steel grades. However, it is less corrosion-resistant compared to other aluminium grades and often requires protective coatings.
Uses:
This alloy is predominantly used in the aerospace industry for highly stressed parts such as aircraft wings and fuselage components. It is also popular in the sporting industry for high-performance bicycles and climbing equipment due to its strength and lightweight nature. In addition, Aluminium 7075 is used in the manufacturing of military-grade weapons and armor.
By understanding the distinct properties and applications of these popular aluminium grades, businesses in Australia can make informed decisions when selecting materials for their specific needs, ensuring optimal performance and cost-effectiveness in their projects.
Choosing the Right Aluminium Grade for Your Project Needs
Selecting the appropriate aluminium grade for your project is crucial to ensuring both performance and cost-effectiveness. Various factors, such as strength, corrosion resistance, workability, and thermal conductivity, play a significant role in determining which grade is the most suitable. In this section, we will explore these factors and how they influence your choice.
Understanding the Application Requirements
Before choosing an aluminium grade, it's essential to fully understand the specific requirements of your project. Consider the following questions:
- What is the primary function of the aluminium in your project? Whether it’s structural, aesthetic, or functional, the intended purpose will heavily influence your choice.
- What environmental conditions will the aluminium face? For instance, will it be exposed to moisture, saltwater, or extreme temperatures?
- What are the weight constraints? Aluminium is often chosen for its lightweight properties, but different grades offer varying degrees of strength-to-weight ratios.
- What are the fabrication requirements? Consider whether the aluminium needs to be bent, welded, or machined.
By answering these questions, you can narrow down the list of potential aluminium grades that might suit your needs.
Common Aluminium Grades and Their Characteristics
Australia offers a wide variety of aluminium grades, each with distinct properties:
- 1100 Aluminium: Known for its excellent corrosion resistance and high thermal and electrical conductivity. It is highly ductile, making it suitable for projects that require intricate forming. However, it has low strength compared to other grades.
- 2024 Aluminium: This grade is known for its high strength and excellent fatigue resistance, making it ideal for aerospace applications. However, it has poor corrosion resistance, so it requires protective coatings if used in corrosive environments.
- 3003 Aluminium: A versatile grade with moderate strength and good corrosion resistance. It is easy to work with and weld, making it a popular choice for general-purpose applications such as cooking utensils and heat exchangers.
- 5052 Aluminium: Offers superior corrosion resistance, especially in marine environments, and is highly formable. It is commonly used in marine applications, automotive fuel tanks, and pressure vessels.
- 6061 Aluminium: Known for its excellent mechanical properties and ease of machinability, this is a versatile grade suitable for structural applications. It offers good corrosion resistance and high strength-to-weight ratio, making it popular in construction and aerospace industries.
- 7075 Aluminium: This grade is one of the strongest available, often used in aerospace and military applications. It has good fatigue resistance but is less corrosion-resistant compared to other grades.
Balancing Cost and Performance
Cost is a crucial factor when selecting an aluminium grade. While higher grades may offer superior properties, they also come with a higher price tag. It’s important to balance the performance requirements with budget constraints. For instance, if corrosion resistance is essential but not high strength, opting for a grade like 5052 might be more cost-effective than 7075.
Fabrication Considerations
The fabrication process can affect the choice of aluminium grade. Some grades are easier to weld, while others may offer better machinability or formability. For projects requiring complex shapes or detailed machining, choosing a grade with good workability, such as 6061, can reduce manufacturing time and costs.
Consulting with Experts
Given the wide range of aluminium grades available, it can be beneficial to consult with material specialists or suppliers. They can provide insights into the latest advancements in aluminium technology and help you select the most appropriate grade for your specific needs.
By considering these factors and understanding the unique properties of each aluminium grade, you can make a well-informed decision that aligns with your project requirements and budget.
In conclusion, exploring the diverse grades of aluminium available in Australia reveals a wealth of opportunities for business owners seeking to optimise their operations and product offerings. Understanding the distinct properties and applications of each grade—from the high-strength 7075 used in aerospace to the versatile 6061 favoured in construction—empowers businesses to make informed choices that enhance performance and efficiency. By selecting the appropriate aluminium grade, companies can achieve a delicate balance between cost-effectiveness and product quality, ultimately enhancing their competitiveness in the market. Additionally, the growing emphasis on sustainability in the industry underscores the importance of considering recycled aluminium options, which not only reduce environmental impact but also align with the evolving demands of eco-conscious consumers. As business owners navigate the complex landscape of aluminium grades, they are well-positioned to leverage these insights to drive innovation, meet customer expectations, and secure a strong foothold in their respective industries.