In the bustling world of construction and home improvement, the choice of materials can impact the longevity, aesthetics, and functionality of your projects. For businesses working with aluminium, particularly aluminium suppliers in Sydney, understanding the nuances of material selection is crucial. Aluminium is a versatile and durable option for roofing, fencing, and structural applications, making it a popular choice across the industry. This guide provides an in-depth look at how to choose the best aluminium for your projects, ensuring that your investments are sound and sustainable.
The first step in making an informed decision is understanding the different grades of aluminium available. Each grade has unique properties that make it suitable for specific applications, whether you need a lightweight, corrosion-resistant, or high-strength option. Following this, we'll explore key factors that should influence your choice, such as strength, durability, and weather resistance—critical considerations for projects exposed to the harsh Australian climate. Finally, we'll examine the best aluminium choices for various applications, helping you select the ideal options for roofing, fencing, and structural needs. By the end of this article, you'll have the knowledge to make confident and effective material choices for your business's next project.
Understanding Aluminium Grades: Which One Suits Your Project?
Aluminium is a widely used material across industries such as construction, automotive, aerospace, and manufacturing. Its lightweight nature, corrosion resistance, and versatility make it a preferred choice for various applications. However, selecting the right aluminium grade is crucial to ensuring the success of a project. Each grade possesses unique characteristics that influence its performance, durability, and suitability for specific environments. By understanding the differences between aluminium grades, businesses can make informed decisions that optimise quality, efficiency, and cost-effectiveness.
What Are Aluminium Grades?
Aluminium grades refer to the different classifications of aluminium alloys, which are grouped into series based on their chemical composition and properties. These grades range from the 1000 to 8000 series, each designed for specific applications. The primary alloying elements—such as copper, manganese, magnesium, silicon, and zinc—determine the strength, corrosion resistance, and workability of the aluminium.
Common Aluminium Grades and Their Applications
1000 Series: Pure Aluminium
The 1000 series contains 99% or more aluminium, making it the purest form available. It is highly resistant to corrosion and offers excellent thermal and electrical conductivity. However, it lacks the strength of alloyed aluminium. This series is best suited for:
- Electrical conductors and wiring
- Chemical and food processing equipment
- Decorative and architectural applications requiring high corrosion resistance
2000 Series: Copper Alloys
Aluminium alloys in the 2000 series are primarily alloyed with copper, significantly increasing their strength and hardness. While offering excellent machinability, these alloys have lower corrosion resistance and often require protective coatings. They are commonly used in:
- Aerospace components
- High-strength structural applications
- Military-grade equipment
3000 Series: Manganese Alloys
The 3000 series contains manganese as the primary alloying element, enhancing corrosion resistance and moderate strength. It is commonly used in applications that require good durability without excessive strength. Popular uses include:
- Roofing sheets and cladding
- Beverage cans and food storage containers
- Heat exchangers and air conditioning systems
4000 Series: Silicon Alloys
The 4000 series contains silicon, which lowers the melting point of aluminium, making it ideal for welding applications. These alloys offer wear resistance and moderate strength, making them suitable for:
- Automotive engine components
- Welding wire and brazing materials
- Structural applications requiring thermal stability
5000 Series: Magnesium Alloys
The 5000 series is known for its excellent corrosion resistance, particularly in marine and coastal environments. The addition of magnesium increases strength without compromising flexibility. These alloys are widely used in:
- Marine and shipbuilding industries
- Automotive panels and fuel tanks
- Architectural applications exposed to harsh weather conditions
6000 Series: Magnesium and Silicon Alloys
The 6000 series offers a combination of strength, corrosion resistance, and workability. With magnesium and silicon as the main alloying elements, these grades provide excellent versatility and weldability, making them ideal for:
- Structural components in construction and engineering
- Piping and transportation systems
- Automotive and aerospace parts requiring a lightweight yet durable material
7000 Series: Zinc Alloys
The 7000 series contains zinc as the primary alloying element, producing the highest-strength aluminium alloys available. These alloys are commonly used in demanding applications requiring extreme strength and fatigue resistance, such as:
- Aerospace structures and aircraft frames
- High-performance sports equipment
- Heavy-duty industrial components
Factors to Consider When Choosing an Aluminium Grade
Strength Requirements
The required strength of the aluminium depends on the specific project application.
- High-strength applications: 2000 and 7000 series (ideal for aerospace and structural components)
- Medium-strength applications: 3000 and 6000 series (suitable for general construction and transportation)
- Low-strength applications: 1000 series (best for decorative and non-load-bearing uses)
Corrosion Resistance
Environmental conditions play a key role in determining the appropriate aluminium grade.
- Marine and high-moisture environments: 5000 series (exceptional corrosion resistance)
- General outdoor exposure: 6000 series (good balance of strength and corrosion protection)
- Indoor or controlled environments: 1000 and 3000 series (sufficient corrosion resistance for mild conditions)
Machinability and Formability
Some projects require aluminium that is easy to cut, shape, or weld.
- Best for welding and forming: 4000 and 6000 series
- Best for machining and milling: 2000 and 7000 series
- Best for general fabrication: 3000 and 5000 series
Cost-Effectiveness
Budget constraints often influence material selection.
- Cost-efficient options: 1000 and 3000 series (ideal for applications where extreme strength is not required)
- Mid-range options: 5000 and 6000 series (good balance of performance and affordability)
- Higher-cost, high-performance options: 2000 and 7000 series (suited for advanced industrial and aerospace needs)
Choosing the right aluminium grade ensures that projects meet strength, durability, and cost expectations while maintaining compliance with industry standards. Understanding these grades allows businesses to make informed material selections that optimise performance and longevity.
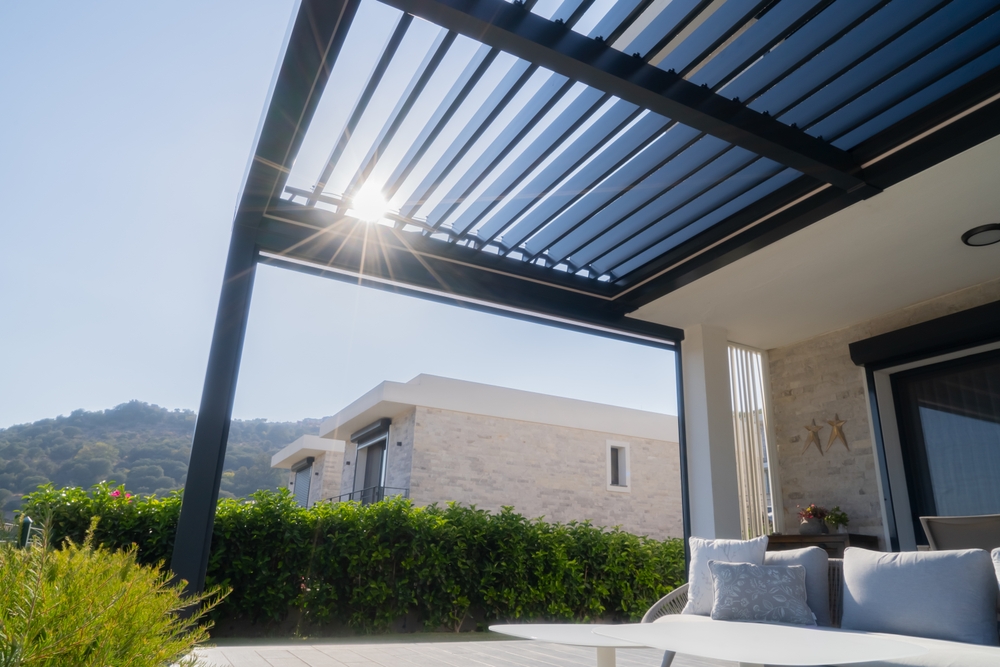
Key Factors to Consider: Strength, Durability, and Weather Resistance
When selecting aluminium for roofing, fencing, and construction, it is essential to assess its performance in terms of strength, durability, and weather resistance. These factors play a crucial role in determining the longevity, reliability, and overall success of a project. Below, we explore these key considerations to help you make an informed decision.
Strength
Aluminium Alloy Composition
The strength of aluminium depends on its alloy composition. Pure aluminium is relatively soft, but when alloyed with elements such as magnesium, silicon, copper, or zinc, its strength increases significantly. The 6000 series (such as 6061 and 6063) and the 7000 series (such as 7075) provide superior tensile strength, making them ideal for structural and load-bearing applications in construction.
Application-Specific Strength Requirements
Different applications require varying levels of strength.
- Roofing: Aluminium used for roofing must be strong enough to withstand snow loads, wind uplift, and thermal expansion. Alloys like 5052 and 6061 provide the necessary strength while remaining lightweight.
- Fencing: Strength in fencing is critical to withstand impact, pressure, and environmental exposure. Alloys such as 6063 offer an excellent balance of strength and flexibility, making them ideal for fencing panels and posts.
- Construction frameworks: For beams, supports, and framing, high-strength alloys like 6061 and 7075 provide excellent load-bearing capacity.
Working with a structural engineer can help determine the most suitable alloy for specific load conditions, ensuring the safety and integrity of your project.
Durability
Corrosion Resistance
One of aluminium’s key advantages is its natural resistance to corrosion, due to the oxide layer that forms when exposed to air. However, the degree of corrosion resistance varies by alloy.
- Marine and coastal environments: Exposure to saltwater and moisture requires marine-grade aluminium, such as 5052 or 5083, known for exceptional corrosion resistance.
- Industrial environments: In settings with exposure to chemicals, pollutants, or humidity, corrosion-resistant alloys like 3003 or 5005 offer a longer lifespan.
- General outdoor use: For roofing, fencing, and architectural structures, the 6000 series provides good corrosion resistance while maintaining strength.
Maintenance and Longevity
Aluminium’s durability extends to its low maintenance requirements. Unlike steel, it does not rust, and with proper surface treatments such as anodising, powder coating, or painting, it maintains its appearance and structural integrity for decades.
- Anodised coatings protect against scratches and corrosion, making them ideal for fencing and outdoor structures.
- Powder coatings provide an extra layer of weather resistance while allowing for custom colour finishes.
- Regular cleaning with mild soap and water is typically enough to maintain aluminium’s finish.
Weather Resistance
Thermal Expansion and Contraction
Aluminium expands and contracts with temperature changes, making it important to choose an alloy that balances thermal stability and flexibility.
- For roofing applications, expansion gaps or floating clip systems can accommodate movement, preventing stress fractures or warping.
- For fencing and structural applications, choosing an alloy with a lower coefficient of expansion, such as 6061, can help maintain long-term stability.
Resistance to UV Radiation and Extreme Weather
Aluminium has high reflectivity, meaning it absorbs less heat from the sun compared to other metals, reducing thermal stress. However, prolonged exposure to UV radiation, extreme heat, and cold can impact coatings and surface treatments.
- For roofing applications, reflective coatings can enhance UV resistance, improving energy efficiency by reducing heat absorption.
- For fencing and outdoor structures, UV-resistant powder coatings prevent fading, chalking, and degradation.
Wind and Impact Resistance
In regions prone to high winds, storms, or hail, selecting an aluminium alloy with high impact resistance is crucial.
- For roofing, alloys like 5052 or 6061 are preferred for their ability to withstand high wind loads and hail damage.
- For fencing, 6063 is commonly used due to its combination of strength and flexibility, allowing it to absorb impact without cracking or bending excessively.
- For structural applications, thicker extrusions or reinforced aluminium framing ensure better wind resistance in high-rise and exposed environments.
Understanding how aluminium performs in different conditions ensures that the right alloy is chosen for roofing, fencing, and construction, leading to a project that is strong, durable, and weather-resistant.
Best Aluminium Choices for Roofing, Fencing, and Structural Applications
Selecting the right aluminium alloy is crucial to ensuring durability, strength, and performance in roofing, fencing, and structural applications. Aluminium’s lightweight yet robust properties make it a highly sought-after material across various industries. Below, we explore the most suitable aluminium options for these applications, helping you make an informed choice that aligns with your project’s requirements.
Aluminium for Roofing
Alloy 3003
Aluminium Alloy 3003 is a widely used roofing material due to its excellent corrosion resistance and ease of fabrication. This alloy contains manganese, which enhances its strength compared to pure aluminium while maintaining flexibility. It is particularly suitable for residential and commercial roofing applications, offering:
- High corrosion resistance, making it ideal for areas with frequent rainfall and humidity.
- Good formability, allowing for easy shaping and installation.
- Lightweight properties that reduce structural load without compromising durability.
Alloy 5052
For projects requiring a stronger and more resilient roofing material, Alloy 5052 is an excellent choice. It is particularly favoured for its:
- Exceptional resistance to marine and coastal environments, making it ideal for locations near the ocean.
- High fatigue strength, ensuring long-term durability under harsh weather conditions.
- Minimal maintenance requirements, reducing long-term costs associated with corrosion and wear.
Aluminium for Fencing
Alloy 6061
Aluminium Alloy 6061 is one of the most versatile fencing materials due to its strong mechanical properties and excellent corrosion resistance. It is commonly used in both residential and commercial fencing applications, offering:
- A balance of strength and flexibility, making it suitable for high-impact environments.
- Superior weather resistance, ensuring durability in outdoor settings.
- Ease of welding and fabrication, allowing for custom fencing designs.
Alloy 6063
Known as the architectural alloy, Alloy 6063 is widely used in decorative fencing applications where aesthetics are as important as functionality. Its key benefits include:
- A smooth surface finish, making it ideal for ornamental fencing designs.
- High corrosion resistance, ensuring longevity even in outdoor environments.
- Anodising capability, allowing for custom colours and finishes that enhance appearance.
Aluminium for Structural Applications
Alloy 2024
For structural applications that demand a high strength-to-weight ratio, Alloy 2024 is a preferred option. While it has lower corrosion resistance than other alloys, it is valued for its:
- High tensile strength, making it suitable for load-bearing structures.
- Excellent fatigue resistance, ensuring long-term performance in demanding environments.
- Common use in aerospace and heavy-duty construction, demonstrating its reliability.
Alloy 7075
When ultimate strength is required, Alloy 7075 stands out. Although primarily used in aerospace and automotive applications, it is also suitable for construction projects where weight reduction is essential. It provides:
- One of the highest strength levels among aluminium alloys, making it ideal for critical structural elements.
- Good machinability, allowing for precision engineering in complex designs.
- The need for protective coatings to enhance corrosion resistance, as it is less resistant to environmental exposure than marine-grade alloys.
Key Considerations for Selecting Aluminium
Choosing the right aluminium alloy depends on several factors, including environmental exposure, structural demands, and aesthetic preferences. When selecting aluminium for your project:
- Assess the environmental conditions, such as humidity, salt exposure, and temperature fluctuations.
- Determine strength requirements, ensuring the material can withstand expected loads and stress levels.
- Consider maintenance and longevity, especially in high-wear applications where corrosion resistance is a priority.
- Consult with aluminium suppliers or material specialists to ensure you select the most suitable alloy for your specific needs.
Understanding these considerations will help you maximise the performance, durability, and cost-effectiveness of your aluminium investment, ensuring a reliable and long-lasting result for your project.
Selecting the right aluminium for roofing, fencing, and construction is a crucial decision that directly influences the durability, efficiency, and overall performance of your project. Understanding the various aluminium grades allows you to choose materials that align with specific functional and environmental requirements, ensuring long-term success.
Key considerations such as strength, corrosion resistance, and weather resilience should guide your selection process. For roofing, prioritising lightweight yet corrosion-resistant alloys ensures easier installation and reduced maintenance over time. In fencing, choosing materials that balance structural integrity with aesthetic appeal enhances both security and visual impact. For structural applications, high-strength alloys provide the necessary load-bearing capacity to create safe and reliable frameworks.
By carefully evaluating these factors, you can make well-informed material choices that enhance project longevity, reduce costs, and deliver superior results. Whether for residential, commercial, or industrial applications, selecting the right aluminium ensures not only compliance with industry standards but also a competitive advantage in an evolving market.